A page from the "Causes of Color" exhibit...
What do sea snails and emperors have in common? (organic pigments)

Although many modern dyes are synthetic, our ancestors managed to obtain a wide spectrum of colors from mineral and animal sources long before chemical equivalents were manufactured. Those most rare and difficult to obtain became symbols of wealth and status.
Dyes and pigments are words we use loosely to describe colors in food, fabrics, paints, and other materials, but in reality their meanings are distinct. Dyes are colored substances that change the color of other materials permanently. They are soluble substances, though some become insoluble after they have been applied. They have a special affinity for the substrate they color. In contrast, pigments are insoluble color particles that require a binding agent to hold them onto the surface of the material being colored.
Sea snails and Tyrian Purple
![]() |
|
The color purple is associated with wealth and royalty. The purple dye of the ancients is one of the oldest pigments known, with its use traced as far back as the 13th century BC. Murexes, types of drilling snails, have a mucus-secreting organ called a hypobranchial gland. Tyrian purple is eked out in small amounts from the mucus of certain marine mollusks. |
Historically, Tyrian purple was extracted from shellfish of the Murex genus, such as Hexaplex trunculus and Murex brandaris. The name comes from the habitat of the mollusks, traditionally harvested near Tyre in the eastern Mediterranean. Extracting purple dye from shellfish was a skill not limited to those living on the shores of the Mediterranean. The color known as Tyrian purple was produced elsewhere, but Phoenicia (present day Lebanon) was famous for the color of its Tyrian purple and became a big production center. The cloth was prized by the Romans, and used in the fine robes of kings and emperors. Contemporary accounts and archaeological data don’t tell us exactly how the prized “blackish clotted blood” color was produced. We do know that production was on a large scale, and began with the hideously smelly process of leaving the mollusks in huge vats to decompose in the sun. The most prized shade of Tyrian purple is thought to have been the product of a double-phased process. Two different snail types were found near Tyre, both producing slightly different colors. Cloth could be dipped once in the indigo dye of one type of marine snail, and once in the purple-red dye of another type.
The fall of Constantinople in 1453 signaled the end of the large-scale dye industry of Tyrian purple, and cheaper dyes such as madder and lichen purple took over. In addition to Tyrian purple, the Phoenicians also made an indigo dye, extracted from a closely related species of marine snail. This color was known as royal blue or hyacinth purple.
In the mid 19th century, William Perkin produced a synthetic purple known as mauveine, bringing purple within reach of the ordinary citizen. The active chemical constituent of Tyrian purple dye, 6,6’-dibromoindigo, was isolated in the early 20th century.
This world-famous textile is a kermes-dyed mantle made in Palermo for the Norman King Roger II of Sicily, in the 12th century.
Insects and crimson dyes
Scale insects have long been used to produce crimson-colored dyes.
Like madder, these dyes are composed of anthraquinone derivatives and are applied using mordants, usually alum, but sometime tin or iron salts, to produce different hues. The anthraquinone derivatives kermesic acid, carminic acid, and laccaic acid are obtained by hot water extraction from the different Coccus insect species. The first of these dyes is orange-red in color, while the other two are red.
Kermes insects (Kermes vermillio, Kermes palestinensis) are scale insects from the Mediterranean region that are parasitic on several species of dryland oak shrubs. A brilliant red dye is extracted from the shell of the female insects, which huddle immobile in clusters on the wood. Their use has been documented since ancient times, when this color was known as the “King’s red” and treasured as a painter’s pigment. The dye is made using kermesic acid, produced by the kermes insects. Cochineal replaced kermes as the red dye of choice when it was brought back to Europe from the “new world” of America. The dyes are comparable in color quality and intensity, but cochineal dye is 10 or 12 times as effective as the kermes dye.
Cochineal (Dactylopius coccus) is an insect very like the kermes insect, and lives on some cacti or prickly pears. The cochineal beetle is a primarily sessile parasite, feeding on moisture and nutrients in the cacti or prickly pears that form its habitat. |
Carmine (made from cochineal insects) is much more concentrated than the traditional red dyes of madder root, kermes, Polish cochineal and brazilwood. It was in high demand throughout Europe, coloring the fabrics of royalty, nobility, and church leaders. For several centuries it was the most important insect dye used in hand-woven oriental rugs. Michelangelo used carmine in his paints, and the dye lent distinction to the uniforms of the British Redcoats (shown here), the Hussars, the Turks and the Royal Canadian Mounted Police.
Cochineal comes from the cochineal insect, which produces carminic acid to protect itself from its insect predators. Carmine dye is made from carminic acid, which is extracted from the female beetles’ body and eggs. This deep crimson dye is used to produce scarlet, orange, and other shades of red, and is found in cosmetics and as a food colorant.
Harvested cochineal insects were killed by immersion in hot water, steam, or baking in an oven. They were then dried and crushed. This method was developed by the Aztec and Mayan people of Central and North America, where the cochineal insects’ natural cactus habitat is found. After Columbus and the colonization of the Americas, demand from Europe increased the scale of production of this highly prized dye. Nowadays, a variety of methods are employed to extract carmine dye.
With the introduction of commercial synthetic dyes in the late 19th century, the natural dye industry began to diminish. A process that involved the intensive manual labor of breeding the cochineal insects and handpicking them was no competition for laboratory production, which became increasingly inexpensive.
However, because of health concerns over synthetic colorants and food additives, there is a renewed interest in natural dyes. Some artists prefer to use natural dyes, creating a market for carmine oil paints and watercolors. Production of cochineal dyes, known to be non-toxic and non-carcinogenic, has once more become viable for applications in medicine, food production, and cosmetics. Cactus crops in Mexico, Guatemala, and the Canary Islands are in use as commercial cochineal production sites. A small number of people are allergic to cochineal, and react with anaphylactic shock symptoms.
One reason cochineal is prized is its stability as a dye. The color remains constant over time, and is one of the most resistant natural colorants to the effects of light, heat and oxidation, even more so than some synthetic colorants. You can identify carmine dyes in food and cosmetics as E120, cochineal, or Natural Red 4 on packaging labels.
Carmine (derived from cochineal) is used to color food and drinks red. Carmine can be found in food such as meat, sausages, processed poultry products (meat products cannot be colored in the United States unless they are labeled as such), bakery products, cookies, desserts, icings, pie fillings, jams, preserves, gelatin desserts, juice beverages, varieties of cheddar cheese, yogurts, ice-cream and other dairy products, sauces and sweets. |
|
![]() Carmine is one of the very few pigments considered safe enough for use in eye cosmetics. The cosmetics industry is a major consumer of insoluble carmine pigment, particularly for hair and skin products, lipstick, face powder, rouge, and blushes. Another major application is to color pharmaceutical products such as ointments and pills. |
Polish cochineal (Porphyrophora polonica), like kermes and cochineal, are sessile, parasitic scale insects. They live on the roots of various herbs - especially those of the perennial knawel - found in Central Europe and other parts of Eurasia. Cochineal was used through the Middle Ages in the Ukraine, Lithuania, and Eastern Europe to supplement or replace the rare and costly kermes red. Harvested just before the females reach maturity, usually around the Saint’s day of John the Baptist, the dye became known as Saint John’s blood. Polish cochineal was used to dye a variety of natural fabrics. The dye itself contains carminic acid with small amounts of kermesic acid.
The scarcity of Polish cochineal and its plant host today may be traced to extensive harvesting over the centuries. Rather than collect the larvae alone, harvesters uprooted the entire plant. Until the introduction of cochineal from the Americas in the 16th century, the Polish cochineal insect was an important trade commodity.
Lac insects produce a red dye very similar to those of the cochineal and kermes insects, but are also known for their production of a glassy resin processed to produce shellac. Also scale insects, the Laccifer lacca or Kerria lacca insects secrete a resin to protect themselves between hatching and maturing into adults. They are found in huge colonies on a variety of trees in Southeast Asia.
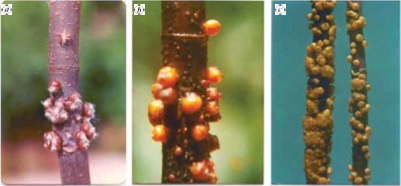
Lac insects on a twig
The encrustation (insects surrounded by resin) attached to the twig is called sticklac and this is scraped from the trees. The water-soluble red dye, which comes mainly from the body of the insect, is obtained by aqueous extraction from the sticklac. The dye consists of laccaic acid or laccaic acid analogs. The residue is processed to produce seedlac and shellac. Processed seedlac and shellac have lower amounts of laccaic acids, but contain the water-insoluble yellow pigment erythrolaccin, which is concentrated in the excreted resin.
Production of shellac, the only commercial natural lacquer, overtook the production of the dye towards the end of the 19th century, when synthetic dyes became widely available. The clearer the lacquer, the higher its quality. Seedlac and shellac are used in a multitude of applications including varnishes, paints, printing inks, sealing wax, micanite compounds, and to coat pills, sweets, and chocolates. Shellac was used in making vinyl records and to color Indian military uniforms. It is still found in oriental carpet dyes. Its gloss enhances nuts, fresh fruit, vegetables, and even jellybeans. Shellac is available in shades from yellow to deep orange, and may be bleached white.
Lac dye is used in a variety of fields, very similar to those where cochineal is used. Natural fabrics such as wool and silk are dyed with lac, it is used in skin cosmetics, and has pharmaceutical applications. The Chinese traditionally use lac to dye leather. With the use of mordants, the color of lac can be adapted to shades of red from violet to brown. Sticklac and its derivatives are still produced today, principally in India, Thailand, and the People’s Republic of China. Minor producers include Bangladesh, Myanmar, Vietnam, and Sri Lanka.
Plant dyes
Many plant pigments are used as dyes. These dyes find uses in the food industry and fabric design, among others. Examples of two, indigo and madder, are discussed below, but the list is extensive.
Indigo
Indigo is a natural dye that is structurally related to betalains. As any fashionista knows, pigment is much more than a dietary necessity. For millennia, plants have been used to make dyes. Indigo is a natural dye with a lineage that can be traced back to the ancient Egyptian city of Thebes in 3000 BC. Egyptian mummies dating back to around 2400 BC were wrapped in cloth that included traces of indigo, and by 2000 BC its use was widespread in India. The Picts, who tried to halt Julius Caesar in Britain in 58 BC, wore blue paint. The dye was obtained either from the indigo plant, or from other European plants, such as woad. Indigo is still widely used in blue jeans, although today it can be produced synthetically, as well as through fermentation of the indigo plant (which is not itself blue).
This diagram of Common Madder (Rubia tinctorum), comes from Thomé, Flora von Deutschland, Österreich und der Schweiz 1885.
Madder
Madder has been used since ancient times as a red vegetable dye for leather, wool, cotton and silk. It can yield pink, orange and purple shades as well as red. There is some evidence suggesting that it was used in Ancient Egypt. While brown and black pigments occur abundantly in nature, red was harder to reproduce and therefore rare and costly. For this reason, red fabric traditionally belonged to royalty.
Madder is extracted from plants of the same family as coffee (Rubiaceae), but from the genus Rubia. Within this genus, Rubia tinctorum produces the highest concentrations of dye. Madder is concentrated in the roots. Madder grows all over the world, including Europe and the Middle East. The uniforms of the British Redcoats were made using madder, but the red produced was susceptible to bleaching by sunlight, and also produced a range of red hues. Accordingly, once cochineal dye was introduced, this more expensive dye was used for the officers’ coats.
To produce the dye, the roots of the madder plant are dried, crushed, and hulled. Many methods exist, but a popular method to extract the dye is to place the hulled root in water (preferably hard water) at low temperatures. Controlling the temperature is critical, as the color can change to browns at higher temperatures (above 200°F). The roots contain alizarin in the form of a glycoside, ruberythric acid. By drying, fermenting, or treating the root with weak acid, the ruberythric acid is hydrolyzed to form alizarin and other products. Some dye preparations also use alcohols or alkaline solutions.
Unlike dyes such as indigo, madder has to be mordanted to fix it in a fabric. Mordants are ingredients that may or may not impart a color to the fiber, but help other colors adhere to the fiber better. A popular method involves dissolving the dye in a hot alum (aluminum potassium sulphate) solution. It is fairly easy to dye animal fibers with madder, but more complicated to dye plant fibers.
Anthraquinones, alizarin, and purpurin are the main components of madder and were identified as being present in the plant in the early 19th century. Alizarin was synthesized in the late 19th century and became one of the first natural dyes to be synthesized. Nowadays, the use of plant dyes is rare, having been substituted with synthetic dyes.